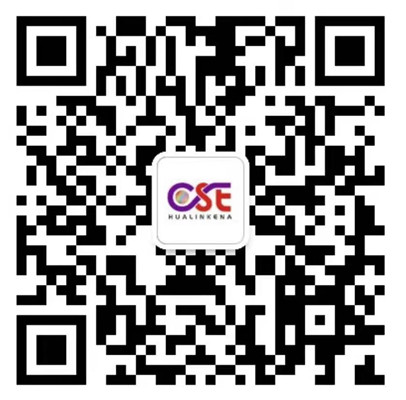
掃碼添加微信,獲取更多半導(dǎo)體相關(guān)資料
微加工過程中有很多加工步驟。蝕刻是微制造過程中的一個(gè)重要步驟。術(shù)語(yǔ)蝕刻指的是在制造時(shí)從晶片表面去除層。這是一個(gè)非常重要的過程,每個(gè)晶片都要經(jīng)歷許多蝕刻過程。用于保護(hù)晶片免受蝕刻劑影響的材料被稱為掩模材料,其用于許多蝕刻步驟中以抵抗蝕刻。該掩模材料可以是光致抗蝕劑,并且使用光刻法將其圖案化。蝕刻也可以稱為制作空腔,這些空腔應(yīng)該根據(jù)用途具有特定的深度。產(chǎn)生的這種空腔的深度可以通過蝕刻時(shí)間和蝕刻速率來控制。執(zhí)行蝕刻機(jī)制的成功之處在于,多層結(jié)構(gòu)的頂層應(yīng)該被完全去除,而在下層或掩模層中沒有任何種類的損傷。這完全取決于兩種材料的蝕刻速率之比,稱為選擇性。在一些蝕刻情況下,蝕刻會(huì)削弱掩模層,并產(chǎn)生形成空腔的傾斜側(cè)壁。底切的距離稱為偏差。
濕法蝕刻是通過使用液體化學(xué)物質(zhì)或蝕刻劑從晶片上去除材料的過程。特定圖案由晶片上的掩模限定。沒有被掩模保護(hù)的材料會(huì)被液體化學(xué)物質(zhì)腐蝕掉。使用光刻技術(shù)在晶片上沉積和構(gòu)圖這些掩模。濕法刻蝕工藝涉及多個(gè)化學(xué)反應(yīng),消耗原有反應(yīng)物,產(chǎn)生新的反應(yīng)物。
濕蝕刻劑通常是各向同性的,并且它們?cè)诤衲のg刻期間導(dǎo)致較大的偏差。它們還需要處理大量有毒廢物。這種蝕刻方法在“后端”處理(BEOL)之前特別有效,在該處理中,晶片在晶片背面研磨之后通常非常薄,并且對(duì)熱或機(jī)械類型的應(yīng)力非常敏感。蝕刻幾微米的非常薄的層將去除在背面研磨過程中產(chǎn)生的微裂紋,導(dǎo)致晶片具有顯著增加的強(qiáng)度和柔性。
這種蝕刻方法快速、簡(jiǎn)單。尖銳各向異性角的倒圓用于避免應(yīng)力集中。這在所有方向上表現(xiàn)出相同的蝕刻速率。橫向蝕刻速率與垂直蝕刻速率大致相同。該蝕刻速率從不依賴于掩模邊緣的方向。
對(duì)于各向同性濕法蝕刻,氫氟酸、硝酸和乙酸(HNA)的混合物是硅最常見的蝕刻劑溶劑。每種蝕刻劑的濃度決定了蝕刻速率。二氧化硅或氮化硅經(jīng)常被用作對(duì)抗HNA的掩蔽材料。當(dāng)反應(yīng)發(fā)生時(shí),材料以類似于向下蝕刻的速度被橫向移除。濕化學(xué)蝕刻通常是各向同性的,即使存在掩模,因?yàn)橐后w蝕刻劑可以滲透到掩模下面。如果方向性對(duì)于高分辨率圖案轉(zhuǎn)移非常重要,通常禁止?jié)穹ɑ瘜W(xué)蝕刻工藝。
?
圖 2 各向同性蝕刻形狀
晶體取向,刻蝕劑的類型,刻蝕劑的溫溫度和濃度都是影響刻蝕的因素。
晶體的取向是影響蝕刻的主要因素之一。在很多情況下,腐蝕的機(jī)理會(huì)因?yàn)榫w取向而受到影響。米勒指數(shù)的概念對(duì)于晶體取向的研究非常重要,因?yàn)樗挥脕碇付ǚ较蚝推矫?。這些方向和平面可以是晶格或晶體。指數(shù)的數(shù)量將與晶格或晶體的尺寸相匹配。
EDP在凸角上的蝕刻速率比其他各向異性蝕刻更快。一般來說,它是底切懸臂的首選。僅僅因?yàn)橥菇堑目焖傥g刻過程表現(xiàn)出拋光作用,它通常會(huì)比其他蝕刻留下更平滑的光潔度。盡管這種蝕刻劑有這么多優(yōu)點(diǎn),但它與金屬氧化物半導(dǎo)體或互補(bǔ)金屬氧化物半導(dǎo)體工藝完全不兼容。因此這種蝕刻劑沒有被廣泛使用,并且對(duì)于各向異性蝕刻工藝,這種蝕刻劑的使用已經(jīng)顯著減少。
TMAH代表四甲基氫氧化銨,這比所使用的所有蝕刻劑更有優(yōu)勢(shì)。這種蝕刻劑顯示出低毒性和CMOS兼容性。盡管使用三甲基氫氧化鉀蝕刻的處理時(shí)間比使用氫氧化鉀要長(zhǎng),但是三甲基氫氧化鉀的使用給我們提供了比氫氧化鉀獲得的蝕刻表面更好的蝕刻表面。由于所有晶體取向的蝕刻速率,使用氫氧化鉀的時(shí)間比使用三甲基氫氧化鉀的時(shí)間短,因此可以獲得完美的晶片正方形。即使對(duì)于包含氫氧化鉀的工藝來說,處理時(shí)間更短,它們也不能提供蝕刻的完美晶片方塊。但是TMAH的優(yōu)點(diǎn)是,即使它需要更多的處理時(shí)間,蝕刻的晶片方塊也將是完美的。各向異性硅蝕刻劑的重要特性是各向異性,選擇性,處理和工藝兼容性。
?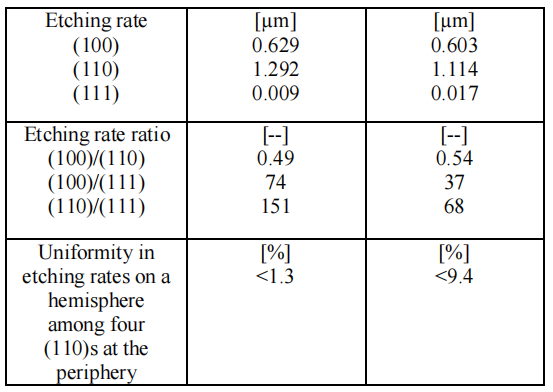
表2氫氧化鉀(中)和TMAH(右)的蝕刻性能
在氫氧化鉀的情況下,使用這種蝕刻劑進(jìn)行蝕刻過程的最佳溫度是80℃,在這種條件下所用的蝕刻劑濃度是35%。這是因?yàn)樵谶@種條件下獲得了具有最小表面粗糙度的最佳蝕刻速率。蝕刻速率與蝕刻劑濃度成反比,與溫度成正比。對(duì)于這種最佳量的蝕刻劑濃度,電鍍蝕刻停止通過生產(chǎn)厚度約為6um的相等量的膜而工作得更好,但是當(dāng)蝕刻劑濃度較低時(shí),電鍍蝕刻停止仍然起作用,但是隨后生產(chǎn)的膜稍微更厚約10 um。硅襯底的摻雜類型對(duì)硅的蝕刻速率幾乎沒有影響,盡管n型蝕刻比p型硅稍快。無論氫氧化鉀溶液濃度如何,二氧化硅蝕刻速率都隨著溫度的升高而不斷增加。使用33重量%的二氧化硅,在80℃下的最大二氧化硅蝕刻速率為450納米/小時(shí)。% KOH。
本文清楚地討論了用于蝕刻工藝的蝕刻劑以及與其各自的濃度和溫度所對(duì)應(yīng)的蝕刻劑的優(yōu)缺點(diǎn)。由于使用的蝕刻劑而進(jìn)行蝕刻的晶圓塊必須在補(bǔ)償結(jié)構(gòu)蝕刻后得到完美的晶圓塊。這個(gè)條件使我們清楚地知道得到完美蝕刻方塊的處理時(shí)間。的一些蝕刻劑受表面活性劑和非離子氫氧化鉀TMAH解決方案,被用來評(píng)估蝕刻性能在各種操作參數(shù)包括蝕刻速率和粗糙度質(zhì)量(100)硅平面,硅溶解的選擇性對(duì)二氧化硅和減少在凸角。蝕刻率隨濃度的增加而降低。隨著濃度的增加,蝕刻表面的粗糙度降低,得到了一個(gè)非常光滑的表面。通過將硅溶解在TMAH溶液中,降低了鋁的蝕刻速率。結(jié)果表明,采用重硼摻雜層或p-n結(jié)的蝕刻停止技術(shù)可適用于TMAH溶液。在添加表面活性劑TMAH的情況下,使用角補(bǔ)償法很難制作出尖銳的邊緣凸角。