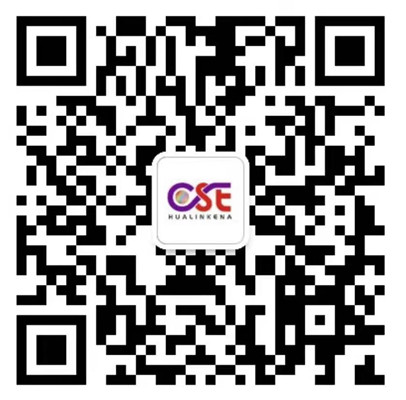
掃碼添加微信,獲取更多半導(dǎo)體相關(guān)資料
在本研究中,開發(fā)了一種包含超聲波和超氣體過程的系統(tǒng),通過調(diào)節(jié)氫氧化銨的功率產(chǎn)生,晶片與超電子換能器間隙中的巨波保證了整個(gè)晶片上均勻的聲能,超氣能促進(jìn)了自由基的產(chǎn)生,從而在稀溶液中去除殘基,與超聲波相比,氫氧化銨溶液中超氣清洗的特征損傷減少。此外,大氣離子清洗產(chǎn)生的氣泡空化的機(jī)械力也提高了殘?jiān)娜コ?,提高了傳質(zhì)速率。極端的空化有利于去除顆粒,但會(huì)破壞晶圓的特性。超聲波清洗造成的損傷明顯大于超氣清洗。
?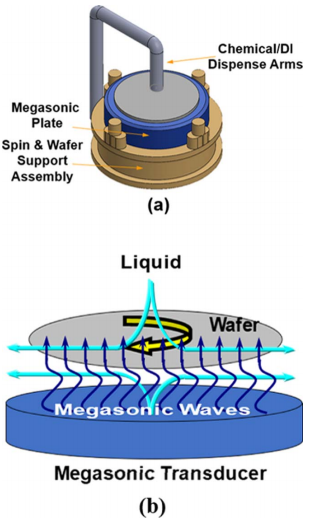
圖1
圖1(a)顯示了本研究的超氣清洗過程示意圖,并顯示了晶片的位置,在晶片的兩側(cè)進(jìn)行巨超聲清洗,在背面進(jìn)行全功率清洗,在單個(gè)晶片清洗板的正面進(jìn)行功率衰減,該自旋清洗工具配有徑向傳感器陣列,用于單晶片的大型濕式清洗,超氣傳感器(面積323mm)設(shè)計(jì)為0.98MHz的自旋基底(通常為0-50rpm),旋轉(zhuǎn)卡盤被設(shè)計(jì)用來容納200毫米的晶圓,用動(dòng)態(tài)光散射法確定的氧化硅顆粒的尺寸為250±50nm,所有實(shí)驗(yàn)均在臺(tái)灣半導(dǎo)體研究所(TSRI)的一個(gè)100級(jí)微/納米制造中心進(jìn)行,圖案樣品在200mm晶片上的晶片自旋清洗組件中暴露在超氣體攪拌中。
實(shí)驗(yàn)研究了標(biāo)稱頻率為80kHz時(shí)的超聲波清洗問題,提高工藝的可重復(fù)性,并確保每個(gè)晶片的新鮮化學(xué)成分,采用雙面清洗,具有不同的正面和背面化學(xué)能力,針對低顆粒進(jìn)行了優(yōu)化,建立了一種由氫氧化銨調(diào)節(jié)功率產(chǎn)生的超聲和超氣過程不同措施的系統(tǒng)。
在聲功率密度為70w的情況下,用pH為8.2的氫氧化銨溶液在30s后進(jìn)行(a)超氣清洗,在30s后進(jìn)行(b)超聲清洗,如果晶片上覆蓋指示性位置的大量區(qū)域被破壞,那就足夠了,通過小顆粒確定了污染位點(diǎn),對于超氣清洗,進(jìn)行PRE以確定清洗能力。首先,計(jì)數(shù)大量超過1μm的粒子,并放置在一個(gè)8英寸的晶片上,然后將晶片放入傳感器設(shè)備中,通過元?dú)鈹嚢杞⑵饋?/span>,然后使用70W的功率清洗晶片以避免污染,溶液以~5.5至6μmmin?1的流量遍布晶片,然后將樣品放入顆粒計(jì)數(shù)器中計(jì)數(shù)清洗后剩余顆粒的數(shù)量。
?
圖3
圖3顯示了在pH值為8.2時(shí),氫氧化銨中發(fā)生的聲功率密度與損傷密度的對比圖,在溶液功率增加后,可以觀察到強(qiáng)烈的損傷,這清楚地表明超氣體系統(tǒng)的損傷明顯低于超聲波系統(tǒng),圖3顯示了用氫氧化銨清洗后的圖案碎片上的損傷部位,在pH值為8.2時(shí),隨著20W功率從20W增加到70W,氫氧化銨的缺陷密度增大,與30s的超聲和超氣體清洗暴露時(shí)間相比,氫氧化銨溶液中超氣體清洗的特征損傷減少。
在超氣清洗之前,可以在二氧化硅的側(cè)壁上清楚地觀察到聚合物殘基。對200毫米晶片進(jìn)行了全晶片試驗(yàn),從而去除了整個(gè)殘留物和顆粒。擴(kuò)展納米技術(shù)的工藝流程,以獲得超氣體攪拌的結(jié)果,超聲有助于在評估超聲攪拌能力的工藝流程中,去除器件晶片中的殘留物,對于互連,物理攪拌處理似乎是優(yōu)先的,只要可以限制去除殘留物所需的蝕刻量,從而使介質(zhì)不損壞。
從等離子體蝕刻條件切換到表面的超氣體條件,有效地減少了碎片的數(shù)量和劃痕的數(shù)量;缺陷的數(shù)量也略有減少,因此,巨超聲清洗似乎可以減少更換標(biāo)準(zhǔn)調(diào)節(jié)器時(shí)的劃痕和缺陷,在側(cè)壁和底部,超聲波后清洗產(chǎn)生沉重的碎片,可以附著在晶片表面,相對于超氣體清洗,超聲波清洗后會(huì)有更多的殘留物粘在表面上。
在氫氧化銨溶液中,殘留位點(diǎn)的大小在~200nm的范圍內(nèi),蝕刻后的殘留物沒有通過超聲波清洗清除,而是通過超氣清洗清除,巨氣清洗60s后,從金屬線側(cè)壁上去除,超氣攪拌的影響也應(yīng)用于PR去除粒子的溶液中,大氣攪拌的使用也有利于防止沉積。此外,超氣攪拌不僅適合于減少缺陷,而且可以增加PR而不需要過強(qiáng)力,從而導(dǎo)致結(jié)構(gòu)損傷。
本文表明,在氫氧化銨中提供高PRE的同時(shí)減少特征損傷,解答大氣清洗產(chǎn)生的氣泡空化的機(jī)械力也提高了傳質(zhì)率,提高了殘?jiān)娜コ芰?/span>,與典型的氧化硅殘留去除方法相比,該方法具有較高的殘留去除效率,且材料損耗低,長寬比高。超氣清洗造成的損傷明顯低于超聲波清洗系統(tǒng),最后,首次成功地證明了純Ge堆疊納米片fet,在60°C下的新型選擇性硅蝕刻,這些結(jié)果表明,超氣清洗可應(yīng)用于納米顆粒清洗過程,巨波清洗正迅速成為集成電路制造過程中后工藝清洗的一種有效方法。