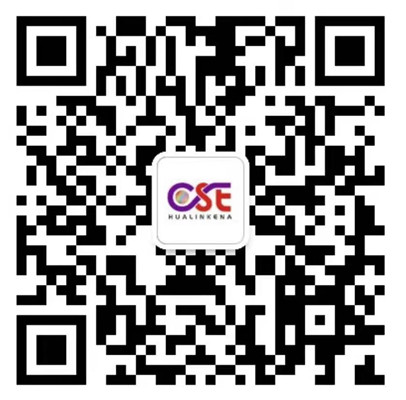
掃碼添加微信,獲取更多半導(dǎo)體相關(guān)資料
引言
高濃縮臭氧氣體已被用來使用通過鹵素加熱器局部加熱的石英爐對(duì)碳化硅單晶基底進(jìn)行干氧化,當(dāng)臭氧的‰低速度保持在5mcm-1或以上時(shí),臭氧的強(qiáng)氧化能力使碳化硅在明顯低于氧氧化的溫度下快速氧化,臭氧氧化也導(dǎo)致MOS結(jié)構(gòu)的器件摩擦化過程中界面態(tài)密度較低,這可能是因?yàn)槌粞跹趸跍p少碳相關(guān)缺陷方面是安全的。
與其他化合物半導(dǎo)體不同, 在SiC上與硅器件一樣,通過熱氧化可以形成氧化硅膜,因此具有比較容易制作MOS結(jié)構(gòu)的優(yōu)點(diǎn),目前只能得到SiC MOSFET的溝道遷移率極低的東西,最近也有通過氧化膜的氮化處理和熱解再氧化等改善界面狀態(tài)的報(bào)告。
為了解決上述問題,實(shí)現(xiàn)低損耗SiC功率MOSFET,各種處理前的氧化膜/SiC的初期界面良好,可以認(rèn)為會(huì)對(duì)后期處理的效果產(chǎn)生影響,為此,認(rèn)為使用臭氧等反應(yīng)性高的氧化物質(zhì)是有效的。即由于臭氧等的高氧化力,形成氧化膜,同時(shí)抑制與碳相關(guān)的界面缺陷的發(fā)生。
圖1是用于臭氧氧化的石英制氧化爐的概略圖。在市售的2個(gè)石英法蘭之間焊接用熔融石英制作的試料加熱部,形成氧化爐管。試料SiC基板放置在氧化爐中可拆卸的不透明石英基座上,通過鹵素?zé)艏訜崞鬟M(jìn)行輻射加熱,基板溫度雖然沒有直接測(cè)量,但在同樣的條件下,通過測(cè)量對(duì)SiC基板進(jìn)行氧氧化(1氣壓)時(shí)的氧化速度進(jìn)行了推定。
?
圖2
高濃度臭氧與高溫容器或配管的內(nèi)壁接觸時(shí),極容易分解成氧氣,發(fā)揮其強(qiáng)氧化力,因此, 為了抑制臭氧的分解,供給到氧化試料領(lǐng)域, 將放置SiC基板的不透明石英基座上的空間盡可能縮?。? mm×24 mm×30 mm),制作了石英爐(圖2)。臭氧的流量是根據(jù)蓄積的臭氧量和在實(shí)驗(yàn)條件下將該臭氧氣化排氣所需的時(shí)間來求出的,在得到特性最好的氧化膜的條件下, 臭氧的流量約為150 sccm(以標(biāo)準(zhǔn)狀態(tài)cm3每分鐘表示的流量),爐內(nèi)部的壓力約為960 Pa,因此臭氧的流速提高到5.2 m·s―1.在Fig.1的系統(tǒng)中,臭氧完全熱分解時(shí)下游的壓力上升率為11,因此臭氧的分解率可以根據(jù)下游的壓力上升率來估計(jì)。將4mm角試料加熱到根據(jù)SiC基板的氧氧化速度推定的1100°C 1,150°C時(shí),在下游加熱前后,爐下游的壓力從810 Pa上升到850 Pa(上升率5),由此可以認(rèn)為實(shí)現(xiàn)了在試料正上方也能確保50 vol.1以上的臭氧濃度的狀態(tài)
?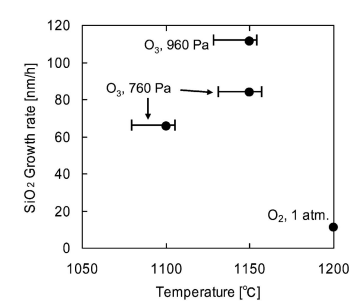
圖3
如圖3所示, 1氣壓氧氧化(1,200°C)下20nm/h以下的氧化膜成長(zhǎng)速度, 960 Pa高濃度臭氧氧化(1,150°C)時(shí)增大到100 nm/h以上,處理時(shí)間大幅縮短,這種氧化速度的大幅增大,與硅氧化一樣,從臭氧中熱解離產(chǎn)生的氧原子成為氧化物質(zhì),氧化膜中的氧化物質(zhì)的擴(kuò)散以及界面上氧化的活化能大幅降低。但是,在12 mm角基板中,臭氧供給的上游側(cè)和下游側(cè),如圖4所示,產(chǎn)生了最大53.7 nm和43.4 nm的膜厚差(約20),此時(shí)爐下游的壓力上升率接近上限11,可以認(rèn)為臭氧幾乎完全熱分解。因此,為了在超過1,000°C的高溫氧化條件下,在12 mm角以上的試料上實(shí)現(xiàn)可靠性評(píng)價(jià)所需的膜厚分布10以內(nèi)的氧化膜的生長(zhǎng),通過取得低頻測(cè)量和高頻測(cè)量的差分,進(jìn)行Dit的計(jì)算,這是利用了一般界面能級(jí)在高頻測(cè)量中不跟隨這一點(diǎn)的方法,在一個(gè)柵極電壓中的高頻和低頻的CV特性中的容量的差分表示Dit 9。在本方法中,如果氧化膜有電流泄漏,則無法測(cè)量正確的蓄積容量,由于任何試料的氧化膜厚度都足夠大,在測(cè)量中使用的柵極電壓中,可以忽略電流泄漏對(duì)Dit的影響。在實(shí)驗(yàn)的圖中(a)的CV特性中,高頻(實(shí)線)和低頻(虛線)的差值與(b)相比較小,這表示在高溫下制作的(a)比(b)Dit低。
在上述MOS電容器的制作中,柵極氧化膜的形成是在氧氣中進(jìn)行的,這是在1氣壓,1,200°C下進(jìn)行的(干氧化膜,厚度為50 nm)。由此可以看出,用高濃度臭氧制作的MOS電容器比用通常的熱氧化制作的MOS電容器顯示出更低的Dit。
從以上可以確認(rèn),通過高濃度的臭氧氧化,在約1,150°C下,以約100nm/h的氧化速度,可以形成界面能級(jí)密度降低的SiC MOS界面。使用能夠以大流速供給反應(yīng)性氣體的石英爐,通過濃縮至約100的減壓臭氧進(jìn)行SiC襯底的干氧化過程的結(jié)果,在約1,150°C的低溫下,實(shí)現(xiàn)了約100nm/h的高速氧化。另外,將氧化的試料制成MOS結(jié)構(gòu),進(jìn)行電特性評(píng)價(jià)的結(jié)果,與1氣壓高溫氧氧化膜相比,確認(rèn)了界面狀態(tài)的改善。這些結(jié)果,由于臭氧的高反應(yīng)性,抑制與碳相關(guān)的界面缺陷的發(fā)生的可能性很高,但是為了闡明機(jī)理,需要膜中碳濃度的測(cè)量等更詳細(xì)的評(píng)價(jià)。