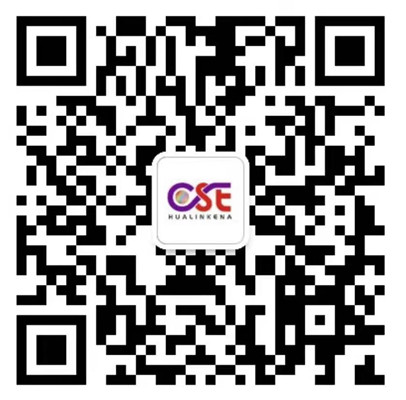
掃碼添加微信,獲取更多半導(dǎo)體相關(guān)資料
兩步半導(dǎo)體電鍍工藝將銅沉積到涂覆有半貴金屬的晶片上,沉積方式在晶片上是均勻的,并且在后電填充退火后沒有空隙。種子層電鍍浴使用獨(dú)特的脈沖波形在非常薄的薄膜中以高密度均勻一致地使銅成核,然后,在第二浴填充特征之前,對晶片進(jìn)行退火。種子層退火提高了半貴金屬與銅界面的粘附性和穩(wěn)定性,并且在后填充退火之后,所得的銅界面保持無空隙。
本發(fā)明總體上涉及用于在晶片上沉積銅的方法和設(shè)備,更具體地說,涉及用于在半導(dǎo)體晶片上電鍍銅種子層的方法和設(shè)備。它對于在鑲嵌和雙鑲嵌集成電路制造方法中電鍍銅特別有用,通過提供一種兩步半導(dǎo)體電鍍工藝來滿足這些需求,在涂有半貴金屬的晶片上形成非常薄且共形的銅種子膜。共形銅種子層的導(dǎo)電性足以用均勻且無空隙的大塊銅對溝槽和通孔進(jìn)行大塊銅電填充。
在本文中使用各種術(shù)語來描述半導(dǎo)體加工工作表面、“晶片和”襯底物可互換使用。通過電化學(xué)反應(yīng)將金屬沉積或鍍在導(dǎo)電表面上的過程通常稱為電鍍或電填充。散裝電填充是指電鍍相對大量的銅,以填充溝槽和溝孔。
?除了使用新的擴(kuò)散屏障材料外,銅種子層的工藝也必須進(jìn)行改變,以克服PVD種子層的局限性。銅籽層的基本要求是連續(xù)的側(cè)壁覆蓋,在功能的頂部有足夠的開口尺寸,以便在電鍍過程中自下而上填充,以及與屏障的良好粘附性。?
首先,討論了一般的銅電鍍硬件和專業(yè)領(lǐng)域,以為本發(fā)明的進(jìn)一步細(xì)節(jié)提供背景。如圖所示1,表示電鍍裝置的圖表橫截面圖。本文詳細(xì)描述了適用于本發(fā)明的具有以下方面的翻蓋式平臺裝置的一般描述。陽極設(shè)置在鍍槽內(nèi)的晶片下方,并通過膜與晶片區(qū)域分離,首選離子選擇膜,陽極膜下面的區(qū)域通常被稱為“陽極室”。
?
圖1?根據(jù)本發(fā)明的電鍍設(shè)備的一個(gè)實(shí)施例的橫截面示意圖
電鍍液通過泵連續(xù)地提供給鍍槽,通常鍍層溶液向上通過陽極膜和擴(kuò)散板流動至晶片的中心,然后徑向向外并穿過晶片。鍍?nèi)芤阂部梢詮腻冸姵氐膫?cè)面設(shè)置到浴液的陽極區(qū)域。然后,如箭頭所示,電鍍?nèi)芤簩㈦婂儾垡绯龅揭绯鲂钏?/span>,然后對電鍍?nèi)芤哼M(jìn)行過濾(未示),并如箭頭所示返回到泵,完成電鍍?nèi)芤旱脑傺h(huán)。
如上所述,當(dāng)電鍍到具有高薄片電阻的薄膜上時(shí),晶片的邊緣和中心之間的沉積厚度會發(fā)生變化。鍍銅電解質(zhì)通常使用銅鹽作為離子源,鹽中的陰離子對溶液的電導(dǎo)率有顯著貢獻(xiàn),影響電解質(zhì)電導(dǎo)率的一個(gè)因素是離子的遷移率,溶液中離子較大的銅鹽的流動性較低,溶液的導(dǎo)電性也較低。一般來說,高度水合或具有超過6個(gè)非氫原子的分子離子足夠大以降低離子在溶液中的流動性,并被認(rèn)為足夠大以降低電解質(zhì)的電導(dǎo)率,與等效濃度的氫等小的高移動離子的影響相比。
通過使用特定的硬件配置來允許在給定的釕薄膜電阻的均勻性要求范圍內(nèi)的厚度分布的電阻率,晶片邊緣與中心之間厚度差的共同均勻性要求的范圍為+/-10%。最好是小于+/-5%。所述電解質(zhì)還包括一種或多種銅配合劑,絡(luò)合劑是結(jié)合溶液中銅陽離子的添加劑,從而增加極化程度,或?qū)~陽離子還原為金屬所需的潛力。由于釕在不同的加工過程(PVD或ALD)中沉積在不同的半導(dǎo)體加工工具上,表面通常被空氣形成的氧化膜覆蓋,未能去除空氣形成的3D氧化物膜可能導(dǎo)致Volmer-Weber(島)在表面生長,所以為了在電鍍槽中實(shí)現(xiàn)連續(xù)的銅成核,通常必須在或接近析氫區(qū)域的負(fù)電位下通過極化去除表面薄膜。
在第一部分中,一些銅被鍍在晶片上;在第二部分中,銅交替地鍍在晶片上并從晶片上取出。結(jié)果表明,這種交替沉積和去除大大提高了成核和覆蓋率。較好的覆蓋范圍降低了給定厚度的銅沉積的電阻率,在脈沖對中的去除脈沖期間,基本上去除在正向脈沖期間沉積的所有銅(例如,先前沉積的銅的至少50%或至少80%)。為了實(shí)現(xiàn)這一目標(biāo)的波形,同時(shí)考慮到正向和反向電流脈沖的電流效率之間的差異,一般來說,正向電流(沉積)的效率低于反向電流(去除),還必須注意不要過度打磨表面。
如上所述,可以沉積在約15~60埃之間的薄保角銅薄膜作為種子層,最小厚度取決于需要在釕表面進(jìn)行連續(xù)覆蓋,以及在整體電鍍步驟之前需要避免銅籽層的完全氧化;第二個(gè)因素可以通過減少種子和批量電鍍步驟之間的時(shí)間和在電鍍步驟之間的環(huán)境中的氧氣暴露來控制。此外,薄片電阻也會影響最小厚度,如果片阻過高,可能無法進(jìn)行批量電鍍,最大尺寸的厚度取決于晶片上特征的幾何形狀。通常,在整體電鍍之前需要小于15,尤其小于10。較高的高寬比增加了特征開口被擠壓而留下未填充空隙的可能性,能夠?qū)⒎浅1〉姆N子層沉積到非常薄的屏障層上,從而可以填充25納米及以下的特征。
圖5A和5B是掃描電鏡的圖形表示,照片包括退火的銅種子層和未退火的銅種子層的疊層的后電填充退火之后的銅金屬化疊層。圖中5B示出了與圖相同層的金屬化堆疊。除了銅種子層,圖中的堆棧。5B包括電鍍和退火的銅種子層,圖中5B中沒有空隙,圖中5A是這種空洞、501、503、505和507的掃描電鏡照片的圖形表示。這些空洞的例子位于特征的不同位置,有不同的大小和形狀,但它們似乎都是在銅-釕界面形成的。
銅電鍍工藝包括可在任何電鍍前預(yù)處理的步驟。由于晶片可能在(預(yù)處理)和電鍍后(電鍍后退火)之前已經(jīng)退火,因此不考慮銅籽層電鍍后的額外退火。在大多數(shù)情況下,晶片在種子層沉積后立即直接轉(zhuǎn)移到大塊電層模塊。
在一段時(shí)間后的環(huán)境條件下,在暴露的銅表面上形成一層氧化銅,當(dāng)暴露在批量電鍍?nèi)芤褐械乃嵝原h(huán)境中時(shí),氧化銅會溶解到電鍍?nèi)芤褐?/span>,這種溶解是不可能的,因?yàn)樗迫チ算~種子層的一部分,這可能使銅種子層不連續(xù)或整體電鍍更加困難。通過在批量電鍍之前的還原環(huán)境中退火晶圓,任何氧化銅都可以潛在地還原為銅金屬。因此,與批量電鍍?nèi)芤汉?/span>t接觸時(shí),銅籽層溶解,并且意外發(fā)現(xiàn)?銅籽層退火減少或消除后電填充退火后形成的空隙,雖然這并不打算受到這一理論的約束,但這認(rèn)為退火種子層可以加強(qiáng)和穩(wěn)定銅/半貴金屬的界面。不均勻或粗糙的半貴金屬覆蓋和/或不均勻的銅籽層覆蓋會導(dǎo)致界面弱,在電填充后退火過程中晶片經(jīng)歷應(yīng)力時(shí),界面弱會導(dǎo)致空隙形成。請注意,氧化銅還原和銅釕界面穩(wěn)定退火不需要具有相同的工藝要求。?
一般來說,在晶片表面實(shí)現(xiàn)鍍銅的均勻厚度分布,鍍過程中晶片表面應(yīng)存在均勻的電壓分布,但為了補(bǔ)償端子效應(yīng),需要通過增加向晶片內(nèi)部區(qū)域提供的電壓或電流來補(bǔ)償電阻性電壓降,從而在整個(gè)晶片表面上保持等效的界面電位?;蛘撸梢赃x擇陽極室開口的形狀以匹配被鍍晶片表面,同時(shí)調(diào)整靠近晶片邊緣的電流通量。
所述電鍍裝置的電解質(zhì)成分的任何修改和新的配置都可用于在具有釕涂層和電鍍種子的晶片上的批量電鍍。特別是,上述結(jié)構(gòu)和電解質(zhì)組合物的組合可以是有效的在一個(gè)實(shí)施例中,低酸電解質(zhì)化學(xué)的硬件配置包括高電極虛擬陽極、雙陰極和鍍槽中的各種介電插入物,以形成電流場。
圖中4描述了作為本發(fā)明的一個(gè)方面的實(shí)施例的電鍍系統(tǒng),該系統(tǒng)包括三個(gè)獨(dú)立的電氣電鍍或電鍍模塊411、417和419。系統(tǒng)tem400還包括三個(gè)獨(dú)立的后電填充模塊(PEMs)4.15和兩個(gè)421的。
電鍍和退火的銅種子層是本發(fā)明的一個(gè)方面。如上所述,電鍍層銅種子層比PVD種子層更保形,顆粒分布均勻,較多。退火的種子層具有改進(jìn)的銅到半貴金屬界面,從而進(jìn)一步的應(yīng)力。例如后電填充退火施加的,不會在堆棧中形成空隙。
退火后的銅籽層也有一些不同的電學(xué)性能。雖然為了清晰起見,省略了各種細(xì)節(jié),但可以實(shí)現(xiàn)各種設(shè)計(jì)替代方案。