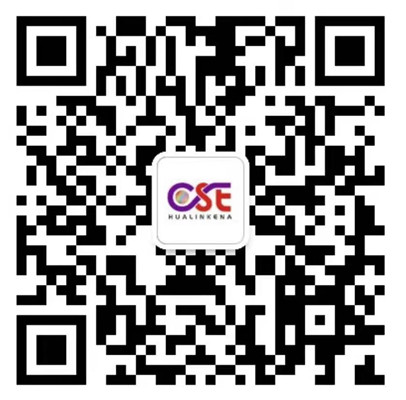
掃碼添加微信,獲取更多半導體相關資料
引言
本文采用超聲增強化學蝕刻技術制備了多孔硅層,利用高頻溶液和硝酸技術在p型取向硅中制備了多孔硅層。超聲檢測發(fā)現(xiàn)p型硅多孔硅層的結構,用該方法可以制備質量因子的多孔硅微腔,超聲波蝕刻所導致的質量的提高可歸因于氫氣泡和其他蝕刻的化學物質從多孔硅柱表面逃逸率的增加。這種效應是由于自由孔載流子濃度的有效變化所致。超聲波顯示,這可能導致了鍵合結構的改變和氧化作用的增加,并建立了超聲處理與微觀結構之間的相關性。
在本研究中,我們報道了在超聲波處理的作用下,通過無靜電蝕刻技術在各種晶片上生長的多孔硅層的結構性能。我們進行了系統(tǒng)的實驗,以確定它們對多孔硅形成的影響。AFM(原子力顯微鏡)和FTIR測量已用于樣品的后續(xù)分析。
?
實驗
化學蝕刻采用p型取向硅,分別在(HF:硝酸:水)中(1:1:2)制備多孔硅層,采用超聲增強(頻率22kHz,US功率30W或50W)化學蝕刻溶液,刻蝕時間為20min。用原子力顯微鏡(AFM)JEOLJSM-IC25S研究了PS的納米結構,采用雙光束Perkin-Elmer850光譜儀測量了PS層的透射率FTIR光譜。結果表明,30W和50W的超聲功率使p型硅的加氫量和氧化量均顯著增加。
?
結果
利用30至50W的不同美國激發(fā),通過(HF和硝酸)溶液制備了多孔硅多孔層,超聲增強蝕刻工藝使蝕刻劑與硅片之間的反應比橫向(各向異性系數(shù)(孔深/孔隙平均寬度)從7.31增加到158.4)。其樣品的AFM圖像如圖-1、(a)-(c)。所示樣品A、B、C的PS層厚度分別為500、1000和1250nm。在相同的有效蝕刻時間下,可以得到兩個明顯的結論:(1)表示樣品的PS層厚度,采用超聲蝕刻(樣品B和C)制備的樣品大于通常采用技術(非超聲)蝕刻(樣品A)制備的樣品。(2)樣品C的硅孔在表面正態(tài)方向上最連續(xù),分布均勻,直徑最小。
?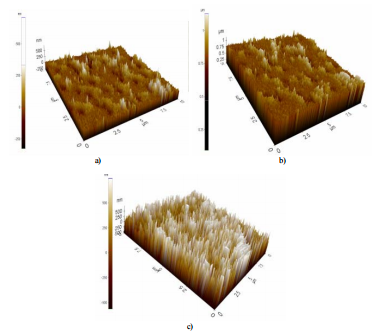
圖-1
樣品的PS層更均勻,硅孔更小,蝕刻效率也高于常規(guī)技術制備的(非超聲)。原因是,簡單采用化學蝕刻法時,化學反應產物會沉積在硅孔,主要在孔尖,防止硅片溶解,從而擴大橫向蝕刻,當超聲波作用于電解質溶液中時,會出現(xiàn)大量的微氣泡,這些氣泡會隨著各種聲壓的變化不斷收縮和膨脹,導致硅柱化學產物脫吸。如果氣泡破裂,則將會產生極高的壓力,這種壓力將把溶解的物質從硅孔中帶出來。此外,其他的超聲波效應,如振動,也會加速化學產物的擴散,這些原因導致化學反應集中在孔隙尖端,從而降低了側向蝕刻,提高了均勻性和蝕刻效率。
采用AFM法測定了三個樣品的平滑度,如圖-1所示。顯微圖中最明顯的現(xiàn)象是硅柱尺寸從樣品C增加,而均勻性減小。4個樣品的表面粗糙度均方根(RMS)值分別為17.324nm(樣品A)、9.505nm(樣品B)和3.779nm(樣品C)。
表1為US蝕刻時間20min后PS層的厚度、蝕刻率、平均尺寸、粗糙度和功率。與低(30W)美國激發(fā)下(平均深度為1000nm)相比,美國功率的增加導致產生更深的孔隙(平均深度為1250nm)。另一方面,如果美國的功率很高(50W),空化過程就是強有力的證據(jù)。
?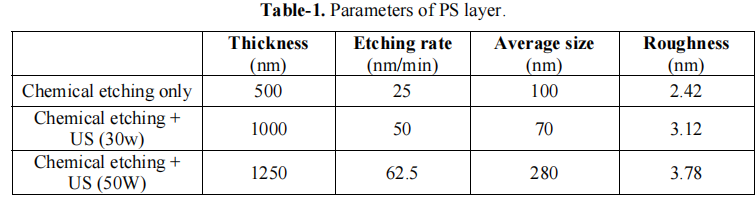
利用FTIR光譜中的透射光譜研究了大孔孔表面的化學組成,在400~4000cm-1不同波長的化學蝕刻制備的新制備的PS層的FTIR透射譜如圖2所示。
PS層形成過程中的超聲處理導致了p型(111)Si的微觀結構特征。從圖中可以看出,新制備的PS層在2400cm-1處有Si-H吸收帶,這些模式與吸附在擴展的PS表面上的基團有關。眾所周知,Si-Hx含量對于鈍化質量是必需的,因為氫可能很容易在PS/Si界面以及在硅晶片內部擴散。樣品的FTIR光譜,其中峰1108cm-1對應于SiOx中SiO-Si橋的拉伸模式,由于該峰值劑量沒有發(fā)生重要的變化,因此可以認為這種模式與硅襯底有關,否則1108cm-1處的模式僅出現(xiàn)在具有一定氧化程度的PS層中,其頻率可能與PS表面缺陷氧化硅的高應力sio2-Si界面有關,這些模是硅橋的對稱和反對稱振動模。
綜上所述,我們提出了一種制備PS層的超聲增強化學蝕刻方法,表面研究原子力顯微鏡(AFM)顯示,當其他蝕刻參數(shù)恒定時,超聲蝕刻會產生更厚、更均勻的PS層,比非超聲化學蝕刻具有更小的硅孔。AFM觀測進一步證實了其改進的結構性質,這可以解釋為PS形成力學,特別是超聲空化。對PS單層和PS微腔的研究表明,超聲蝕刻優(yōu)化了樣品的特性,將超聲蝕刻與常用技術相結合,獲得了質量最佳的樣品,這種新型蝕刻方法是制備PS材料,特別是PS多層材料的高效技術,為實現(xiàn)PS材料的應用開辟了可行的途徑。