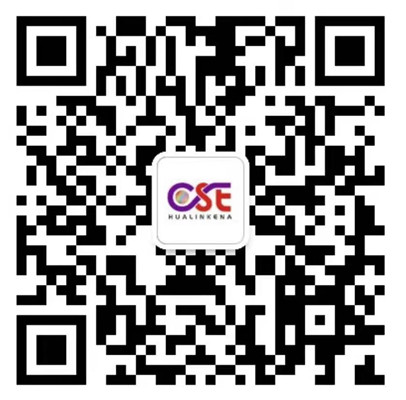
掃碼添加微信,獲取更多半導(dǎo)體相關(guān)資料
引言
? ? ? 本研究將三維安裝過程 為了實(shí)現(xiàn)高品質(zhì)、低成本, 我們的目的是建立高通量,無損傷的濕加工工藝技術(shù)及其制造設(shè)備技術(shù)的基礎(chǔ)。 關(guān)于通過濕法蝕刻使硅晶圓變薄的問題, 為了提高作為課題的蝕刻速度和蝕刻均勻性,明確要控制的參數(shù)。 將對其進(jìn)行高精度控制的要素技術(shù)導(dǎo)入到旋轉(zhuǎn)方式的片葉濕法蝕刻裝置中, 利用大口徑的硅晶圓,明確了其效果。另外, 進(jìn)行加工后的晶圓評(píng)價(jià), 在加工后的晶圓上, 不存在損傷層(破碎層、微裂紋、晶體缺陷等); 強(qiáng)度沒有降低; 并且,確認(rèn)裝置的電氣特性沒有變動(dòng), 另外,對加工后的晶圓進(jìn)行了評(píng)價(jià),確認(rèn)了加工后的晶圓中不存在損傷層,為了防止Cu的污染,可以維持襯墊氧化膜,以及器件的電特性沒有變動(dòng),確立了適用于三維疊層半導(dǎo)體工藝的通過濕法蝕刻形成硅貫通電極的技術(shù)的基礎(chǔ)。另外,通過實(shí)現(xiàn)本目的, 晶圓減薄和插拔可以在同一裝置中實(shí)施。
?
實(shí)驗(yàn)
? ? ? 由于傳統(tǒng)技術(shù)的背面研磨的硅晶圓的減薄會(huì)產(chǎn)生損傷,雖然進(jìn)行了損傷去除,但是存在無法去除的深度的損傷,因此發(fā)現(xiàn)了確立不產(chǎn)生減薄加工損傷的無損傷的減薄工藝的必要性,提出了通過濕法蝕刻的硅晶圓的減薄。另外,作為不使用干法蝕刻的硅貫通電極形成工藝,提出了通過濕法蝕刻的硅貫通電極形成。
? ? ? 關(guān)于硅晶圓的減薄,敘述了可以適用于三維積層半導(dǎo)體工藝的通過濕法蝕刻的硅晶圓減薄技術(shù)的基礎(chǔ)的確立。具體來說,整理了所要求的條件,其結(jié)果,根據(jù)所要求的蝕刻速度等,選擇了使用混酸溶液(HNO3+HF)的工藝。由于使用混酸藥液的濕法蝕刻是強(qiáng)放熱反應(yīng),所以利用高溫狀態(tài)下的反應(yīng),進(jìn)行控制,通過適用旋轉(zhuǎn)方式的濕法蝕刻裝置,確立了可以適用于三維積層半導(dǎo)體工藝的通過濕法蝕刻的硅晶圓減薄技術(shù)的基礎(chǔ)。
? ? ? 關(guān)于蝕刻速度的提高,發(fā)現(xiàn),通過對化學(xué)液體濃度(成分)的蝕刻速率的確認(rèn),可以用市場上的化學(xué)液體獲得足夠的蝕刻速度;通過對化學(xué)液體溫度的蝕刻速率的確認(rèn),可以通過提高溫度來提高蝕刻速度;通過應(yīng)用自旋蝕刻工藝,可以通過液體的切換效果和反應(yīng)產(chǎn)物的排除效果來提高蝕刻速度。實(shí)現(xiàn)了1920μm/min,而不是350μm/min的蝕刻速度目標(biāo)值。此外,考察了混合酸的高速蝕刻反應(yīng),并提出了一種新的反-180-反應(yīng)機(jī)制。
? ? ? 關(guān)于蝕刻均勻性的提高, 混酸溶液的反應(yīng)是強(qiáng)烈的放熱反應(yīng), 在藥液與晶圓接觸期間,即使發(fā)生放熱反應(yīng),也有必要進(jìn)行控制,使溫度變化變小。 預(yù)先設(shè)定為規(guī)定溫度以上的晶片溫度, 為了改良片葉旋轉(zhuǎn)濕法裝置,進(jìn)行了要素技術(shù)的改良。對加工后的硅晶圓進(jìn)行了評(píng)價(jià)。通過斷面觀察,通過濕法蝕刻進(jìn)行減薄加工后的缺陷較少。通過彎曲強(qiáng)度測量,通過濕法蝕刻進(jìn)行減薄強(qiáng)度最高,強(qiáng)度低的東西較少。制作了6英寸CMOS晶圓,通過對減薄前后的器件特性的評(píng)價(jià),證實(shí)了成為問題的電特性的變動(dòng)沒有。
? ? ? 關(guān)于硅貫通電極的形成, 闡述了可應(yīng)用于三維積層半導(dǎo)體工藝的濕法蝕刻形成硅貫通電極技術(shù)的基礎(chǔ)的確立。 選擇了使用堿性溶液的工藝,該工藝適合于提高硅和作為硅貫通電極的保護(hù)膜的襯氧化膜(TEOS―SiO2)之間的蝕刻選擇比。 可以提高與襯墊氧化膜的選擇比。 蝕刻速度低是一個(gè)課題。 為了實(shí)現(xiàn)高速蝕刻, 雖然有應(yīng)用于MEMS加工用途的例子, 沒有實(shí)際應(yīng)用, 另外,在TSV插塞工藝以及旋轉(zhuǎn)方式的濕法蝕刻中沒有適用事例。 使用添加了羥胺(NH2OH)作為蝕刻加速劑的堿溶液。 為了提高蝕刻速度,提出了使用羥胺溶液作為加速劑,這在TSV插塞工藝中沒有應(yīng)用實(shí)例,并將其添加到TMAH溶液和KOH溶液中,以提高蝕刻速度作為效果,并通過添加NH2OH的KOH溶液實(shí)現(xiàn)了3μm/min或更高的蝕刻速度,這是蝕刻速度的目標(biāo)值。此外,考察了添加NH2OH溶液增加蝕刻速率的原因,發(fā)現(xiàn)添加NH2OH溶液和不添加NH2OH溶液的反應(yīng)機(jī)制不同,并提出了添加NH2OH溶液時(shí)使用KOH溶液進(jìn)行蝕刻的反應(yīng)機(jī)制。
? ? ? 關(guān)于提高蝕刻的均勻性, 堿溶液的蝕刻, 雖然不是強(qiáng)烈的放熱反應(yīng), 由于晶圓溫度的均勻性和藥液量的均勻性是必要的, 除了化學(xué)液的溫度控制外,還提出了在蝕刻前加溫硅晶圓,相對于蝕刻均勻性的目標(biāo)值±8%以下,達(dá)到±1%?!ぴu(píng)價(jià)加工后的硅晶圓,觀察表面粗糙度,不產(chǎn)生成為問題的粗糙度。通過截面觀察,在通過濕法蝕刻形成貫通電極后,缺陷較少。作為襯氧化膜TEOS―SiO2的陰影―181―響聲,確認(rèn)Si和襯氧化膜的選擇比,有50:1以上的選擇比。通過觀察濕法蝕刻形成的TSV的截面,不使襯氧化膜消失。評(píng)價(jià)器件特性,證實(shí)了通過濕法蝕刻形成的TSV在電特性上沒有問題。
?
討論和結(jié)果
? ? ? 為了與半導(dǎo)體集成電路的性能·功能的進(jìn)一步提高不同,使用了三維層疊多個(gè)集成電路芯片的半導(dǎo)體工藝技術(shù),通過將異種或同種集成電路芯片薄化、三維安裝的層疊技術(shù),縮短芯片間距離,降低信號(hào)傳播所需的布線長度,從而實(shí)現(xiàn)高速化, 另外,通過增加單位容積收容芯片數(shù)量和種類,實(shí)現(xiàn)小型化、大容量化、多功能化.其中,使用硅貫通電極的三維層疊半導(dǎo)體工藝技術(shù)的開發(fā)正在積極進(jìn)行,但在現(xiàn)有技術(shù)中,硅片的薄化工藝和 在那里,從硅片加工面到深度10ym以上的傾城都生成了機(jī)械缺陷,另外,硅貫通電極從硅片背面的露出工序未能在短時(shí)間內(nèi)高精度地進(jìn)行,本論文以這樣的背景為依據(jù), 開發(fā)了在短時(shí)間工序中不產(chǎn)生機(jī)械缺陷的新的濕加工工藝技術(shù)和為了實(shí)現(xiàn)該技術(shù)的旋轉(zhuǎn)方式的單張濕加工裝量技術(shù),總結(jié)了適用于三維層疊半連體工藝的成果。
? ? ? 針對利用硝酸、佛酸混酸藥液的濕蝕刻的硅片薄化技術(shù),明確了為了兼顧高蝕刻速度和高均勻性而控制的工藝條件和要素技術(shù),開發(fā)了應(yīng)用該技術(shù)的旋轉(zhuǎn)方式的單片濕蝕刻裝置, 使用相對于藥液濃度的變化,蝕刻速度的變化變小的濃度范圍的混合酸藥液,同時(shí)將從線性淋浴噴嘴供給的藥液的溫度保持在80℃,并且從晶片背面?zhèn)裙┙o90℃的純水,從而直徑達(dá)到200mm 蝕刻連度1920um/mim和蝕刻均勻性1.9% .另外,在濕蝕刻后晶片上不生成破碎層微裂紋結(jié)晶缺陷等機(jī)械缺陷,且抗彎強(qiáng)度不降低,在濕蝕刻前后。
? ? ? 關(guān)于硅貫通電極的硅片背面露出技術(shù),為了兼顧高蝕刻速度和硅對硅貫通電極的保護(hù)膜即攤派氧化膜的高蝕刻選擇性, 提出了向堿性藥液中導(dǎo)入作為蝕刻加速劑發(fā)揮效果的羥胺溶波.適用于旋轉(zhuǎn)方式的單片濕蝕刻裝置.使用大口徑的硅片明確了其效果.
研究表明,蝕刻均勻性達(dá)到+1%,加工后的晶片無機(jī)械缺陷生成,能夠在硅晶片整個(gè)表面上殘留復(fù)氧化膜,以及硅貫通電極的漏電流無變動(dòng),這是極其重要且有用的成果。