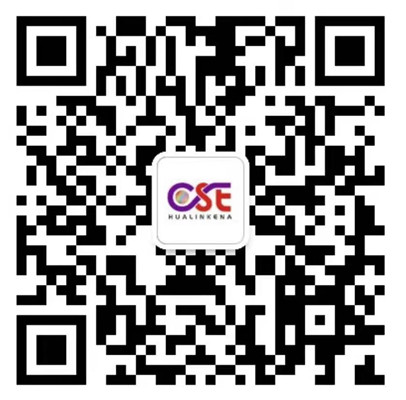
掃碼添加微信,獲取更多半導(dǎo)體相關(guān)資料
引言
? ? ? 微加工過(guò)程中有很多加工步驟。蝕刻是微制造過(guò)程中的一個(gè)重要步驟。術(shù)語(yǔ)蝕刻指的是在制造時(shí)從晶片表面去除層。這是一個(gè)非常重要的過(guò)程,每個(gè)晶片都要經(jīng)歷許多蝕刻過(guò)程。用于保護(hù)晶片免受蝕刻劑影響的材料被稱(chēng)為掩模材料,其用于許多蝕刻步驟中以抵抗蝕刻。該掩模材料可以是光致抗蝕劑,并且使用光刻法將其圖案化。蝕刻也可以稱(chēng)為制作空腔,這些空腔應(yīng)該根據(jù)用途具有特定的深度。產(chǎn)生的這種空腔的深度可以通過(guò)蝕刻時(shí)間和蝕刻速率來(lái)控制。執(zhí)行蝕刻機(jī)制的成功之處在于,多層結(jié)構(gòu)的頂層應(yīng)該被完全去除,而在底層或掩模層中沒(méi)有任何種類(lèi)的損傷。這完全取決于兩種材料的蝕刻速率之比,稱(chēng)為選擇性。在一些蝕刻情況下,蝕刻會(huì)削弱掩模層,并產(chǎn)生形成空腔的傾斜側(cè)壁。底切的距離稱(chēng)為偏差。
?
蝕刻類(lèi)型
? ? ? 各向同性蝕刻:濕蝕刻劑通常是各向同性的,并且它們?cè)诤衲のg刻期間導(dǎo)致較大的偏差。它們還需要處理大量有毒廢物。這種蝕刻方法在“后端”處理(BEOL)之前特別有效,在該處理中,晶片在晶片背面研磨之后通常非常薄,并且對(duì)熱或機(jī)械類(lèi)型的應(yīng)力非常敏感。蝕刻幾微米的非常薄的層將去除在背面研磨過(guò)程中產(chǎn)生的微裂紋,導(dǎo)致晶片具有顯著增加的強(qiáng)度和柔性。
? ? ? 對(duì)于各向同性濕法蝕刻,氫氟酸、硝酸和乙酸(HNA)的混合物是硅最常見(jiàn)的蝕刻劑溶劑。每種蝕刻劑的濃度決定了蝕刻速率。二氧化硅或氮化硅經(jīng)常被用作對(duì)抗HNA的掩蔽材料。當(dāng)反應(yīng)發(fā)生時(shí),材料以類(lèi)似于向下蝕刻的速度被橫向移除。濕化學(xué)蝕刻通常是各向同性的,即使存在掩模,因?yàn)橐后w蝕刻劑可以滲透到掩模下面。如果方向性對(duì)于高分辨率圖案轉(zhuǎn)移非常重要,通常禁止?jié)穹ɑ瘜W(xué)蝕刻工藝。
? ? ? 各向異性濕法蝕刻:液體蝕刻劑根據(jù)哪個(gè)晶面暴露于所使用的蝕刻劑,以不同的速率蝕刻晶體材料。蝕刻速率的巨大差異取決于硅晶面。當(dāng)使用類(lèi)似硅的材料時(shí),這種elTect可以允許非常高的各向異性。制造各種微機(jī)械器件的關(guān)鍵技術(shù)是各向異性蝕刻。各向異性蝕刻中的蝕刻速率在蝕刻平面中快得多,因?yàn)槲g刻時(shí)間通常在硅的(111)平面中進(jìn)行。各向異性蝕刻的重要因素包括選擇性、處理和工藝兼容性以及各向異性。各向異性濕法蝕刻產(chǎn)生約1 μm/分鐘的典型蝕刻速率。
?
影響蝕刻的因素
? ? ? 基于晶體的取向:晶體的取向是影響蝕刻的主要因素之一。在很多情況下,腐蝕的機(jī)理會(huì)因?yàn)榫w取向而受到影響。米勒指數(shù)的概念對(duì)于晶體取向的研究非常重要,因?yàn)樗挥脕?lái)指定方向和平面。這些方向和平面可以是晶格或晶體。指數(shù)的數(shù)量將與晶格或晶體的尺寸相匹配。
? ? ? 基于蝕刻劑的類(lèi)型:蝕刻劑EDP代表乙二胺-鄰苯二酚。電子數(shù)據(jù)處理蝕刻很容易被二氧化硅、氮化硅、金、鉻、銀、銅和鉭掩蓋,但電子數(shù)據(jù)處理可以蝕刻鋁。這種蝕刻劑具有很強(qiáng)的腐蝕性和致癌性,而且蝕刻量不如氫氧化鉀。這種蝕刻劑會(huì)腐蝕附近的任何金屬。它會(huì)在難以去除的表面留下棕色污漬。與其他各向異性蝕刻相比,EDP在凸角上的蝕刻速率更快。盡管這種蝕刻劑有這么多優(yōu)點(diǎn),但它與金屬氧化物半導(dǎo)體或互補(bǔ)金屬氧化物半導(dǎo)體工藝完全不兼容。因此這種蝕刻劑沒(méi)有被廣泛使用,并且對(duì)于各向異性蝕刻工藝,這種蝕刻劑的使用已經(jīng)顯著減少。
? ? ? 基于蝕刻劑的溫度和濃度:在氫氧化鉀的情況下,使用這種蝕刻劑進(jìn)行蝕刻過(guò)程的最佳溫度是80℃,這種條件下的蝕刻劑濃度是35%。這是因?yàn)樵谶@種條件下獲得了具有最小表面粗糙度的最佳蝕刻速率。蝕刻速率與蝕刻劑濃度成反比,與溫度成正比。對(duì)于這種最佳量的蝕刻劑濃度,電鍍蝕刻停止通過(guò)生產(chǎn)厚度約為6um的相等量的膜而工作得更好,但是當(dāng)蝕刻劑濃度較低時(shí),電鍍蝕刻停止仍然起作用,但是隨后生產(chǎn)的膜稍微更厚約10 um。
? ? ? 硅襯底的摻雜類(lèi)型對(duì)硅的蝕刻速率幾乎沒(méi)有影響,盡管n型蝕刻比p型硅稍快。無(wú)論氫氧化鉀溶液的濃度如何,二氧化硅的蝕刻速率隨著溫度的升高而不斷增加。使用33重量%的二氧化硅,在80℃下的最大二氧化硅蝕刻速率為450納米/小時(shí)。% KOH。鋁蝕刻速率在最大蝕刻速率為3.0微米/分鐘的所有氫氧化鉀濃度下都是可感知的。隨著氫氧化鉀濃度和鍍液溫度的增加,蝕刻后的硅表面變得平滑。硅表面粗糙度隨著蝕刻持續(xù)時(shí)間的增加而降低,這是由于蝕刻過(guò)程中產(chǎn)生的氫氣泡被掩蔽,這大大增加了表面粗糙度。
? ? ? 使用這種蝕刻劑的蝕刻過(guò)程在90℃的溫度下進(jìn)行。這是因?yàn)?,該工藝的最佳溫度范圍?0℃—90℃,但最佳蝕刻速率只能在該特定范圍內(nèi)的最高溫度值下獲得。蝕刻劑濃度取為25%,因?yàn)榧內(nèi)谆h(huán)己烷會(huì)導(dǎo)致嚴(yán)重的底切]。使用25%濃度的另一個(gè)具體原因是因?yàn)楸砻娲植诙入S著TMAH濃度的增加而降低,并且僅用25% TMAH獲得光滑表面。即使在這里,蝕刻速率也隨著蝕刻劑濃度的增加而降低,并且蝕刻速率隨著溫度而增加。
? ? ? 與氫氧化鉀(35%)情況下的濃度使用相比,三氧化二氫(25%)情況下的蝕刻劑濃度使用較少,但代價(jià)是處理時(shí)間增加。還可以評(píng)估(100)、(110)和(111)晶面的蝕刻速率對(duì)溫度和濃度的依賴(lài)性、對(duì)二氧化硅和S13N4的選擇性、鋁蝕刻速率對(duì)溶解硅量的依賴(lài)性、多晶硅蝕刻速率對(duì)硼濃度的依賴(lài)性以及電化學(xué)蝕刻特性。實(shí)驗(yàn)表明,蝕刻速率隨著濃度的增加而降低。當(dāng)重量百分比為5%時(shí),蝕刻表面有時(shí)被金字塔形小丘覆蓋,蝕刻速率變得非常低。隨著濃度的增加,蝕刻(100)表面的光滑度急劇變化。當(dāng)重量百分比為5%時(shí),表面覆蓋有高密度的金字塔形小丘。隨著濃度從5重量%增加到15重量%,小丘的密度降低并且獲得更小的小丘。超過(guò)22重量%,獲得非常光滑的表面。22 wt %溶液的測(cè)量粗糙度在100 nm以?xún)?nèi)。粗糙度對(duì)溫度沒(méi)有顯著的依賴(lài)性。隨著濃度從5重量%增加到22重量%,粗糙度變小,并且在30重量%時(shí)獲得相當(dāng)光滑的表面。
? ? ? 鋁的蝕刻速率表明,溶解硅的量增加,鋁的蝕刻速率降低。當(dāng)溶解硅超過(guò)40 g/l時(shí),鋁腐蝕速率迅速下降。對(duì)于67 g/l的溶解硅,獲得了0.01的鋁蝕刻速率。
?
表七?各種蝕刻速率(微米/分鐘)和蝕刻溫度(100)晶體取向
總結(jié)
? ? ? 用于蝕刻工藝的蝕刻劑連同蝕刻劑的優(yōu)點(diǎn)和缺點(diǎn)根據(jù)它們各自的蝕刻劑濃度和執(zhí)行蝕刻工藝的溫度被清楚地討論。由于所使用的蝕刻劑而經(jīng)歷蝕刻的晶片方塊必須在補(bǔ)償結(jié)構(gòu)被蝕刻掉之后獲得完美的晶片方塊。這一條件使我們清楚地了解獲得完美蝕刻方塊的加工時(shí)間。一些蝕刻劑是表面活性劑和非離子的氫氧化鉀和三氧化二氫溶液,用于評(píng)估各種操作參數(shù)下的蝕刻性能,包括(100)硅平面的蝕刻速率和粗糙度質(zhì)量、硅溶解對(duì)二氧化硅的選擇性和減少凸角處的底切。(100)和(110)的蝕刻速率隨著濃度的增加而降低。隨著濃度的增加,蝕刻表面的粗糙度降低,獲得非常光滑的表面。通過(guò)將硅溶解在TMAH溶液中來(lái)降低鋁的蝕刻速率。證實(shí)了使用重硼摻雜層或p-n結(jié)的蝕刻停止技術(shù)適用于TMAH溶液。可以得出結(jié)論,TMAH是一種很有前途的硅微加工解決方案。