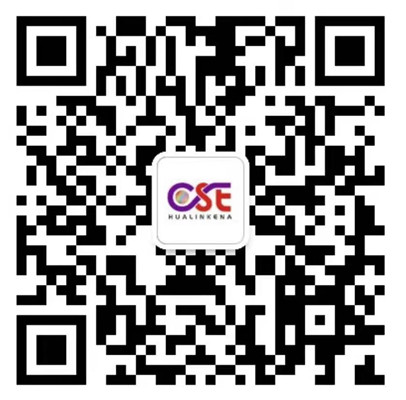
掃碼添加微信,獲取更多半導體相關資料
引言
近年來,小尺寸、輕重量、低生產(chǎn)成本和可再現(xiàn)的可制造性的器件變得非常重要。通過濕法蝕刻單晶硅或玻璃的微機械加工可以符合這些嚴格的要求。硅或玻璃的濕法蝕刻是體微機械加工的關鍵技術,用于生產(chǎn)微器件,如壓力傳感器的隔膜、光纖對準的V形槽和生物芯片的微通道。
隨著微機電系統(tǒng)市場的增長,基于濕法刻蝕的體微操作的精確控制越來越受到關注。特別是,蝕刻表面的粗糙度變化可能是微機電系統(tǒng)器件商業(yè)化中最主要的因素之一。此外,為了通過使用粘合技術組裝微機械零件來制造微器件,需要光滑且無缺陷的表面。
為了改善濕法刻蝕的特性,制作了兆頻超聲波攪拌組件。在本方法中,在有和沒有兆頻超聲波攪動的濕法蝕刻過程中,研究了MAM的特性。MAM的使用改善了濕法蝕刻的特性,例如蝕刻速率、蝕刻均勻性和表面粗糙度。特別地,在硅和玻璃兩種情況下,整個晶片上的蝕刻均勻性都小于1%。通常,單晶硅的初始均方根粗糙度(Rrms)小于0.5 nm。一些研究者通過磁力攪拌和超聲波攪拌分別獲得了566和66 nm的粗糙度。在這項研究中,蝕刻硅表面的粗糙度小于60納米。用兆頻超聲波攪拌濕法蝕刻硅可以在蝕刻過程中保持幾乎原始的表面粗糙度。結(jié)果表明,大氣攪拌是提高蝕刻率、蝕刻均勻性和表面粗糙度的有效途徑,所開發(fā)的微加工系統(tǒng)適用于制造復雜結(jié)構的器件。
?
實驗
樣品的起始材料為6英寸。(100)的硅晶片和一個6英寸的玻璃晶片(石英)。分別使用氮化硅(2000A?)和多晶硅(3000A?)用于遮蔽。蝕刻窗口的每個尺寸為2±2 mm2。為了評價兆頻超聲波攪拌濕法蝕刻的特性,在各種工藝條件下進行蝕刻實驗,即蝕刻時間、兆頻超聲波功率和溶液溫度。在這里介紹的所有情況下,溶液的濃度是相同的。在硅和玻璃樣品的每種情況下,所有的蝕刻實驗分別在30重量%的氫氧化鉀溶液和10∶1的氫氟酸溶液中進行。表2總結(jié)了工藝參數(shù)。蝕刻的表面用顯微鏡和掃描電子顯微鏡檢查。觸筆輪廓測量儀和原子力顯微鏡;自動探針用于表面測量。
?
表2 過程參數(shù)
?
結(jié)果和討論
氣體攪拌的影響:硅和玻璃樣品分別在66C的30wt%氫氧化鉀溶液中和室溫下的10:1HF溶液中蝕刻。巨波能被均勻地應用于一個6英寸的能量上。晶圓片應用的能量密度為4.4W/cm2。如圖10所示,大氣攪拌蝕刻特性優(yōu)于無大氣攪拌蝕刻特性。加和不加巨氣攪拌的蝕刻率分別為0.48和0.46mm/min。特別是,硅和玻璃樣品的蝕刻均勻性在1%內(nèi)。在硅樣品中,大氣攪拌的蝕刻表面粗糙度比沒有大氣攪拌的表面粗糙度小十分之一,大氣攪拌的平均粗糙度(RSave)小于70nm。
?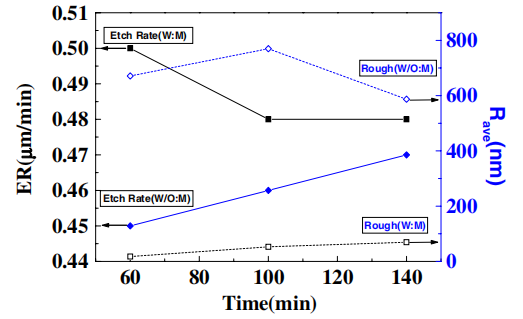
圖10 巨氣攪拌的影響
圖11和圖12顯示了蝕刻硅樣品的顯微鏡和掃描電鏡圖像。氣泡(氫)脫離和流體攪拌對蝕刻表面粗糙度的強烈影響。如圖所示。11(a)和12(a),蝕刻表面光滑且無缺陷。
兆頻超聲波攪拌強度的影響:如前所示,通過兆頻超聲波攪動改善了濕法蝕刻的特性。先前的結(jié)果表明,兆頻超聲波攪動增加了氫泡從硅上的分離e?ciency和蝕刻溶液的刷新率。
圖14顯示了蝕刻過程中兆頻超聲波攪動強度的e?ect。隨著所施加能量的強度增加,(100)硅的蝕刻速率也增加?;咨蠚馀莼蝾w粒的去除力很大程度上取決于顆粒直徑和流動速度,它們分別與聲波的強度和頻率成比例。隨著施加的兆頻超聲波能量的增加,表面很容易脫落,蝕刻速率得到提高。
溶液溫度和蝕刻線性:圖15顯示了蝕刻速率、溶液溫度和巨氣攪拌之間的關系。一般來說,蝕刻速率隨著溶液溫度的升高而增加。如圖所示,當應用巨氣攪拌時,也得到了相同的結(jié)果。在所有溫度下,有大攪拌的粗糙度都小于沒有大攪拌的粗糙度。無論溶液溫度是否升高,巨氣攪拌都能有效地提高蝕刻特性。
圖16顯示了大氣攪拌蝕刻過程中蝕刻深度的線性度。當蝕刻深度呈線性擬合時,影響因子r2幾乎等于1。這說明蝕刻深度與蝕刻時間成線性正比,巨氣攪拌不影響蝕刻速度的線性。在蝕刻過程中,表面粗糙度略有增加。蝕刻深度保持了蝕刻過程中1%的均勻性。
?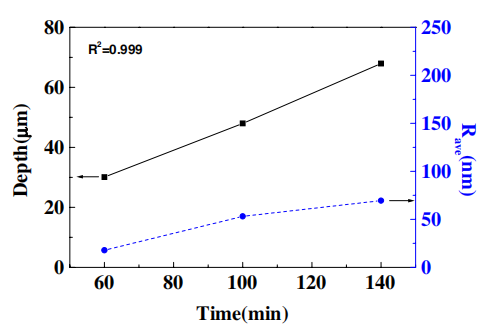
圖16 蝕刻的時間線性
總結(jié)
對于微機電系統(tǒng)器件的制造,硅或玻璃的蝕刻表面必須光滑、無缺陷且尺寸均勻性高。在這項研究中,我們通過兆頻超聲波攪拌改善了蝕刻特性,即蝕刻均勻性、蝕刻速率、表面粗糙度和無缺陷表面。通過(100)硅在氫氧化鉀溶液中的各向異性濕法腐蝕和玻璃在氫氟酸溶液中的濕法腐蝕來評價其特性。特別地,來自MAM的兆頻超聲波能量顯著改善了蝕刻表面的粗糙度和均勻性。在這里,我們提出了在刻蝕過程中使用MAM保持原始表面粗糙度的最佳方法,如表4所示。在不久的將來,我們將把{110}Si蝕刻的特性與Nusse的結(jié)果進行比較,并進一步評估高維結(jié)構器件的制造。
?