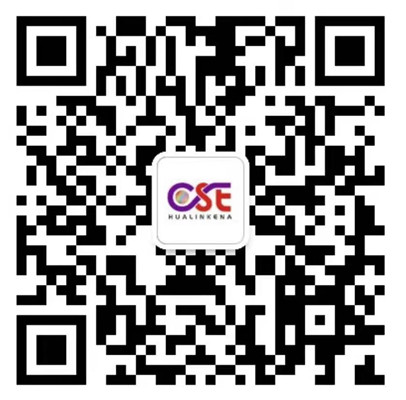
掃碼添加微信,獲取更多半導(dǎo)體相關(guān)資料
引言
? ? ? 薄晶片已經(jīng)成為各種新型微電子產(chǎn)品的基本需求。其中包括功率器件、分立半導(dǎo)體、光電元件和用于射頻識別系統(tǒng)的集成電路。機械研磨是最常見的晶圓減薄技術(shù),因為其減薄率很高。新的微電子產(chǎn)品要求硅晶片厚度減薄到150米以下。機械研磨仍然會在晶片表面產(chǎn)生殘留缺陷,導(dǎo)致晶片破裂,表面粗糙。因此,化學(xué)蝕刻法主要用于生產(chǎn)具有所需厚度的光滑表面的可靠的薄晶片。
? ? ? 在本工作中,我們研究了在硝酸和氫氟酸的混合溶液中,不同硝酸濃度對硅片總厚度和重量損失、刻蝕速率、形貌和結(jié)構(gòu)特性的影響。結(jié)果表明,隨著硝酸濃度和刻蝕時間的增加,總厚度和失重增加。較高的硝酸濃度導(dǎo)致較高的蝕刻速率,并且蝕刻速率隨著蝕刻時間的延長而降低。隨著刻蝕時間和硝酸濃度的增加,光學(xué)顯微鏡觀察到更平滑、更清晰的均勻硅表面圖像。XRD分析表明,腐蝕后硅片的強度比純硅片高,這可能表明腐蝕后表面形成更光滑。本文的研究結(jié)果對生產(chǎn)一種可靠的、理想的、在集成電路制造中至關(guān)重要的硅晶片具有參考價值。
?
材料和方法
? ? ? 使用的化學(xué)品是硝酸,高頻,乙醇,丙酮和蒸餾水。所有儀器在干燥前都用蒸餾水沖洗,以確保所有使用的儀器沒有任何污染物。在蝕刻之前,硅晶片經(jīng)歷溶劑清洗過程,目的是去除其表面的油和有機殘留物。首先用丙酮和乙醇清洗晶片。對于丙酮,它會留下自己的殘留物,因此乙醇被用來清除丙酮殘留物。將丙酮倒入玻璃燒杯中,并在溫度高達55℃的攪拌器熱板上加熱。然后將晶片放入含有乙醇的水浴中10分鐘。然后將晶片從浴中取出,放入乙醇中5分鐘。然后將晶片在蒸餾水中漂洗,并在空氣中進一步干燥。
? ? ? 該化學(xué)品由不同濃度的蝕刻劑混合物組成,這些混合物是恒定濃度的氟化氫和不同濃度的硝酸。在本研究中,使用三種不同的蝕刻劑濃度來研究化學(xué)蝕刻對硅晶片的影響,其中對于每個硅晶片,20重量%、23重量%和26重量%的硝酸蝕刻劑濃度與48重量%的氟化氫蝕刻劑濃度混合。因此,有三組不同的蝕刻劑濃度混合物:HF 48重量% /硝酸20重量%,HF 48重量% /硝酸23重量%,HF 48重量% /硝酸26重量%,體積比為1∶1。每個硅晶片被蝕刻70分鐘,時間間隔為10分鐘。
?
結(jié)果和討論
? ? ? 圖1和圖2分別顯示了在三種不同硝酸濃度為20wt%、23wt%和26wt%HF混合的硅的總厚度和重量減輕與蝕刻時間的關(guān)系。這兩個圖都表明,與蝕刻20wt%硝酸蝕刻的硅片相比,23wt%和26wt%硝酸蝕刻濃度的硅片的總厚度和重量損失增加得更快,硝酸蝕刻濃度是它們中最低的。從圖中可以看出,總厚度和減重量隨著蝕刻時間的增加而增加。在20wt%硝酸濃度下蝕刻的晶片厚度隨蝕刻時間沒有任何顯著變化。然而,23%和26%的總厚度損失顯著增加,總厚度損失為43.06%,其中最高,20%和23%硝酸的總厚度損失分別為16.67%和39.40%。在26wt%硝酸蝕刻濃度下的蝕刻使硅片變薄成440μm,最終重量為0.3501mg。此外,在26wt%硝酸濃度下,厚度損失變化曲線比其他濃度更陡,這表明硅片上發(fā)生的刻蝕過程更快,積極地耗散了樣品厚度。
?
圖1?總厚度損失與蝕刻的關(guān)系
?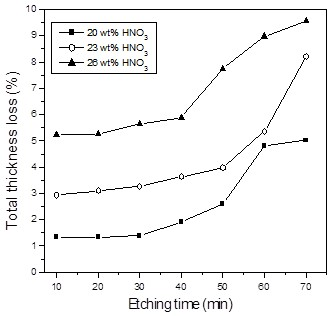
圖2?總重量損失與蝕刻時間的關(guān)系
? ? ? 在本研究中,由于硅片的初始厚度僅為660μm。因此,基于目前的結(jié)果,48wt%HF/26wt%硝酸的硅片總厚度和減重的百分比變化提供了最佳的硅變薄效果,這是微電子器件所必需的。
總結(jié)
? ? ? 綜上所述,浸入硝酸和HF混合物中的厚度和重量的蝕刻率隨著蝕刻時間和硝酸蝕刻濃度的增加而增加。在較高的蝕刻時間和硝酸濃度下蝕刻時,觀察到光滑均勻的硅結(jié)構(gòu)。XRD結(jié)果表明,蝕刻硅片的強度高于純1個硅片并且隨著蝕刻時間的增加而增加。與其他材料相比,用26%硝酸和48%HF的混合物蝕刻的硅片具有最佳的蝕刻率。目前的蝕刻研究表明,蝕刻硅可以潛在安裝到更薄的包裝用于微電子產(chǎn)品的制造。