單晶硅片KOH堿刻蝕工藝研究
在太陽能電池片制造行業(yè)中,通常單晶硅片需要進(jìn)行清洗,去除各種雜質(zhì),或者利用化學(xué)品對(duì)硅片行刻蝕后形成特定的表面狀態(tài),這樣才能夠繼續(xù)進(jìn)行后續(xù)工藝生產(chǎn)。其中,利用堿溶液KOH進(jìn)行刻蝕清洗,是一種重要的硅片處理方式。在濕法設(shè)備中集成多種化學(xué)品后,可以在單個(gè)設(shè)備上完成刻蝕、清洗等不同工藝,達(dá)到對(duì)硅片進(jìn)行綜合處理的目的。KOH溶液的質(zhì)量分?jǐn)?shù)、刻蝕時(shí)間等對(duì)硅片表面狀態(tài)有重要影響。KOH刻蝕過程中需要使用大量的化學(xué)品,近年來隨著技術(shù)的進(jìn)步,出現(xiàn)了KOH堿刻蝕輔助添加劑,通過在KOH溶液中混合輔助添加劑,不僅能夠達(dá)到原先的工藝要求,還能夠有效減少化學(xué)品用量,降低化學(xué)品廢液的處理量和難度,為今后KOH堿刻蝕大規(guī)模用提供了條件
1 實(shí)驗(yàn)材料和工藝
實(shí)驗(yàn)中,使用砂漿切割和金剛線切割的單晶硅片外觀尺寸為156mm×156mm,厚度為200um,電阻率為1-3Q·cm。該單晶硅片為市場(chǎng)常見硅片。電池片生產(chǎn)工藝采用車間量產(chǎn)的PERC(射極純化及背電極)單晶生產(chǎn)工藝。各類化學(xué)品原液質(zhì)量分?jǐn)?shù)如表1所示。

2 實(shí)驗(yàn)結(jié)果與討論
2.1KOH預(yù)清洗
砂漿切割的硅片表面有大量的切割損傷和各種雜質(zhì)等“,需要進(jìn)行清洗才能開展下一步擴(kuò)散工藝。通常采用KOH刻蝕的方式來對(duì)硅片進(jìn)行預(yù)清洗,去除硅片表面各種臟污雜質(zhì)等,達(dá)到清洗效果。清洗工藝中,通??涛g時(shí)間對(duì)工藝效果影響較大。實(shí)驗(yàn)中,保持KOH溶液質(zhì)量分?jǐn)?shù)18%不變,反應(yīng)溫度為70℃,通過改變硅片刻蝕時(shí)間,觀察刻蝕后硅片的外觀影響。刻蝕后硅片外觀見圖1.
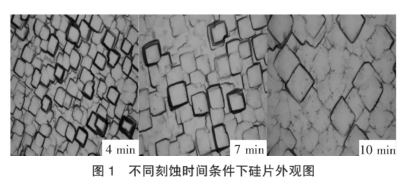
在不同的刻蝕時(shí)間下,刻蝕后硅片表面塔基底座尺寸不一樣,測(cè)量尺寸如表2所示。
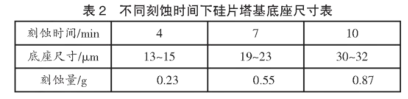
隨著刻蝕時(shí)間的增加,硅片的刻蝕量逐漸增加,塔基底座的尺寸也逐步增大。通常在電池生產(chǎn)中,要求塔基的尺寸也逐步增大。通常在電池生產(chǎn)中,要求塔基的尺寸為20μm±5μm,要求保證一定的刻蝕量,從而達(dá)到清洗效果。同時(shí),刻蝕量還不能過高,過高的刻蝕量會(huì)導(dǎo)致硅片變薄,后續(xù)工藝中碎片率增大,降低生產(chǎn)良率。不同刻蝕時(shí)間下電池片效率對(duì)比如表3所示。
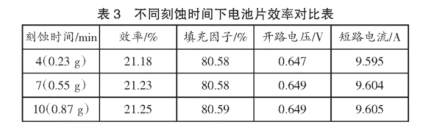
在較高刻蝕量條件下(0.55g和0.87g),電池片效率差只有0.02%,高刻蝕量(0.87g)并沒有帶來電池片效率的明顯提升。同時(shí),低刻蝕量(0.23g)條件下,電池片效率比0.55g條件下低0.05%,主要體現(xiàn)為Ua(開路電壓)低0.002V.(短路電流)低0.009A,說明在低刻蝕量條件下,硅片表面的雜質(zhì)和臟污并沒有完全去除干凈,導(dǎo)致硅片鈍化效果較差,降低了電池片效率,證明硅片的預(yù)清洗是電池生產(chǎn)中的重要工藝。實(shí)驗(yàn)結(jié)果表明,為保證電池最終的轉(zhuǎn)換效率,需要保持一定的刻蝕量(0.55g)。在車間實(shí)際生產(chǎn)中,為保證電池片良率,通常不采用高刻蝕量工藝生產(chǎn)在KOH預(yù)清洗工藝中,需要根據(jù)實(shí)驗(yàn)結(jié)果和生產(chǎn)狀況選取合適的刻蝕量。
2.2清洗后硅片表面黑點(diǎn)
在砂漿切割硅片預(yù)清洗后檢測(cè)外觀時(shí)發(fā)現(xiàn)、在硅片表面出現(xiàn)了數(shù)量不一的黑點(diǎn),如圖2所示。不同廠商的硅片經(jīng)過刻蝕后表面都出現(xiàn)了黑點(diǎn),對(duì)比不同刻蝕時(shí)間的硅片發(fā)現(xiàn),在刻蝕時(shí)間較短的情況下,黑點(diǎn)情況嚴(yán)重,出現(xiàn)了大量的黑點(diǎn);而在刻蝕時(shí)間較長(zhǎng)的情況下,黑點(diǎn)情況大為改善,數(shù)量很少。
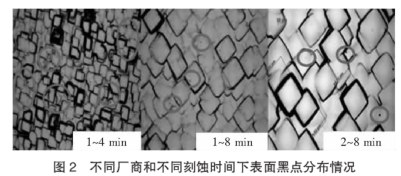
選取不同廠商金剛線切割的硅片進(jìn)行短時(shí)間刻蝕,刻蝕后發(fā)現(xiàn),金剛線切割單晶硅片表面基本沒有發(fā)現(xiàn)黑點(diǎn)現(xiàn)象,見圖3。
即使在較短的刻蝕時(shí)間條件下(4min),也沒有出現(xiàn)明顯的黑點(diǎn)殘留現(xiàn)象。結(jié)合車間調(diào)試過程中出現(xiàn)的部分異常現(xiàn)象,進(jìn)一步進(jìn)行實(shí)驗(yàn)測(cè)試,結(jié)果如圖4所示。
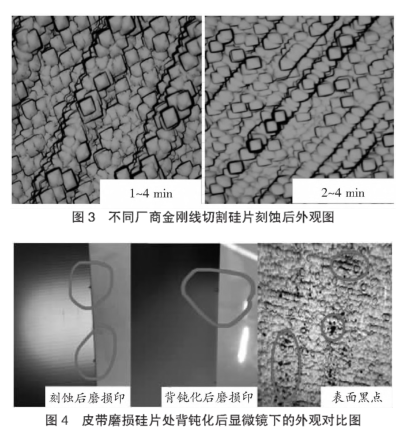
選取金剛線切割單晶硅片,在鏈?zhǔn)皆O(shè)備下料端,傳送皮帶對(duì)硅片有較嚴(yán)重的摩擦,外觀能看到有損傷痕跡。經(jīng)過背鈍化工藝之后,外觀磨損依然嚴(yán)重,肉眼可見磨損痕跡,如圖4所示。顯微鏡放大后可以看到在磨損區(qū)域有大量的黑點(diǎn),而在同一片硅片其余沒有皮帶損傷痕跡的位置,則沒有出現(xiàn)黑點(diǎn)。通過對(duì)比可以推斷,金剛線切割硅片在皮帶磨損處的黑點(diǎn)是硅片與皮帶摩擦帶來的,是一種外部的污染。因此,可以推斷砂漿切割單晶硅片出現(xiàn)的黑點(diǎn)是硅片在進(jìn)行KOH刻蝕前帶來的,并不是刻蝕工藝制程本身帶來的異常。通過查閱砂漿切割硅片的工藝過程發(fā)現(xiàn),該工藝主要是SiC(碳化硅)顆粒在鋼線和硅片之間摩擦滾動(dòng),達(dá)到切制目的,后續(xù)經(jīng)過清洗后成為成品硅片。在此過程中,硅片表面難免會(huì)殘留部分SiC顆粒,因此,可以判斷砂漿切割硅片表面出現(xiàn)的黑點(diǎn)為SiC顆粒。而金剛線切割硅片使用的是鋼線上黏結(jié)金剛石顆粒叫,沒有SiC成分,經(jīng)過KOH刻蝕后,硅片外觀沒有出現(xiàn)黑點(diǎn)現(xiàn)象。
砂漿切割硅片經(jīng)過長(zhǎng)時(shí)間刻蝕后黑點(diǎn)減少,是因?yàn)?/span>SIC主要?dú)埩粼诠杵砻?,?jīng)過長(zhǎng)時(shí)間的刻蝕后,硅片刻蝕量大,表面去除層更多,因此硅片表面殘留的黑點(diǎn)會(huì)更少可見,刻蝕清洗能夠有效去除硅片表面雜質(zhì),是電池片生產(chǎn)中的-項(xiàng)重要工藝。
2.3添加劑堿刻蝕
近年來,發(fā)展出了新的刻蝕輔助添加劑方式進(jìn)行刻蝕,在原有的koH配比基礎(chǔ)上加入部分添加劑,可以大幅度減少KOH的使用量。具體配比如表4所示。
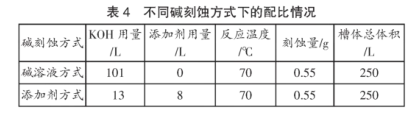
在堿溶液刻蝕方式下,要達(dá)到相同的刻蝕量(0.55g),需要在槽體中添加KOH約101L,而使用添加劑堿刻蝕方式后,KOH的用量?jī)H僅為13L,堿用量的減少可以大大降低工業(yè)生產(chǎn)成本和排廢處理成本。金剛線切割硅片擴(kuò)散后酸刻蝕和添加劑堿刻蝕后外觀對(duì)比見圖5。
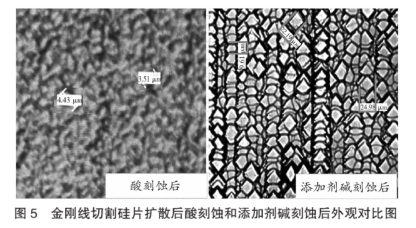
圖5分別為HNO3+HF混酸處理方式(目前常用的擴(kuò)散后硅片處理方式)和添加劑堿刻蝕處理方式的硅片外觀圖,酸刻蝕后硅片表面呈不規(guī)則外觀,無明顯特征,是類似顆粒狀的形貌,顆粒尺寸為4~5um,而添加劑堿刻蝕后的硅片表面塔基底座尺寸與堿溶液刻蝕后基本一致,添加劑堿刻蝕方式完全可以代替堿溶液刻蝕方式。不同處理方式下硅片反射率對(duì)比見圖6。

圖6是硅片制絨、混酸處理和添加劑堿刻蝕后硅片反射率對(duì)比圖。在同樣的刻蝕量條件下,酸處理的硅片表面反射率為38%,而添加劑堿刻蝕后硅片表面的反射率較高,為46%,比酸處理方式高8%,制絨后的反射率為11%,說明在保持外觀形貌和刻蝕量基本一致的條件下,添加劑堿刻蝕處理方式能夠更大幅度地提高硅片反射率。不同處理方式下電池片效率她表5所示。
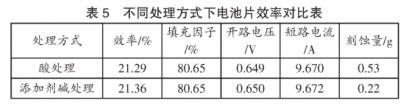
酸刻蝕和添加劑堿刻蝕處理的硅片經(jīng)過后續(xù)工藝電池片效率出現(xiàn)明顯變化。如表5所示,相較于目前常見的混酸處理方式,添加劑堿刻蝕的電池片效率更高,主要體現(xiàn)在U和1的提升上。添加劑堿刻蝕后,硅片反射率提高,可以使背面AI2O3更好地純化硅片,降低電池片背面負(fù)荷,提高PERC單晶電池的轉(zhuǎn)換效率[4-5]。在刻蝕堿質(zhì)量對(duì)比實(shí)驗(yàn)中,添加劑堿刻蝕方式只需要
0.22g(酸處理方式下約41%的比例)的刻蝕量就能提高背面反射率,提高轉(zhuǎn)換效率。同時(shí),更低的刻蝕量還會(huì)降低后續(xù)工藝硅片的碎片率,在電池生產(chǎn)中將會(huì)有更廣泛的應(yīng)用。
3結(jié)語
a)隨著刻蝕時(shí)間的增加,硅片減重量逐漸增大,外觀塔基底座的尺寸也逐漸增大。電池片效率研究結(jié)果表明,刻蝕量對(duì)電池片效率有極大影響。在實(shí)際生產(chǎn)中,需要選擇合適的刻蝕量對(duì)硅片進(jìn)行清洗,刻蝕量過低,硅片表面未能完全清洗干凈,電池片效率低;而過高的刻蝕量會(huì)導(dǎo)致電池片變薄,后續(xù)工藝碎片增多,降低生產(chǎn)良率。
b)砂漿切割的硅片表面會(huì)殘留部分SiC顆粒,在清洗過程中,可以通過延長(zhǎng)刻蝕時(shí)間來去除,但是長(zhǎng)刻蝕時(shí)間下硅片刻蝕量增大,對(duì)后續(xù)工藝有負(fù)面影響。金剛線切割硅片經(jīng)過刻蝕后則沒有SiC雜質(zhì)殘留,從硅片潔凈度角度看,金剛線切割硅片表面殘留物更少,硅片潔凈度更高,在生產(chǎn)上更具優(yōu)勢(shì)。
c)添加劑堿刻蝕方式下,使用少量的KOH就可以達(dá)到工藝要求的刻蝕量,在規(guī)?;a(chǎn)中,不僅可以節(jié)省大量的KOH,還可以降低堿溶液廢水的處理難度。添加劑堿刻獨(dú)方式下PERC電池片效率比酸處理方式下高0.07%,硅片背面反射率提高,改善了電池鈍化效果。同時(shí),添加劑刻蝕方式下反射率提高后,比酸處理方式下的刻蝕量更少,硅片減薄量也更少,添加劑堿處理方式將會(huì)有更好的應(yīng)用前景。(免責(zé)聲明:文章來源于網(wǎng)絡(luò),如有侵權(quán)請(qǐng)聯(lián)系作者刪除。)